前回の「部品図バラシの概要(パート1)」では、部品図バラシの基本概念や設計製造の観点から見たポイントについてご紹介しました。部品図バラシは、単に組立図から個別の部品を切り出す作業ではなく、加工方法や組立工程を考慮した上で、正確で分かりやすい図面を作成するための重要なプロセスです。
今回のパート2では、より実務的な視点から、部品図バラシを進める際の標準や手順、図面作成時の細かな注意点について詳しく解説します。実際の現場で役立つポイントをまとめていますので、設計者・バラシ担当者の方はぜひ参考にしてください。
それでは、部品図バラシの具体的なプロセスやチェックポイントについて、順を追って見ていきましょう。
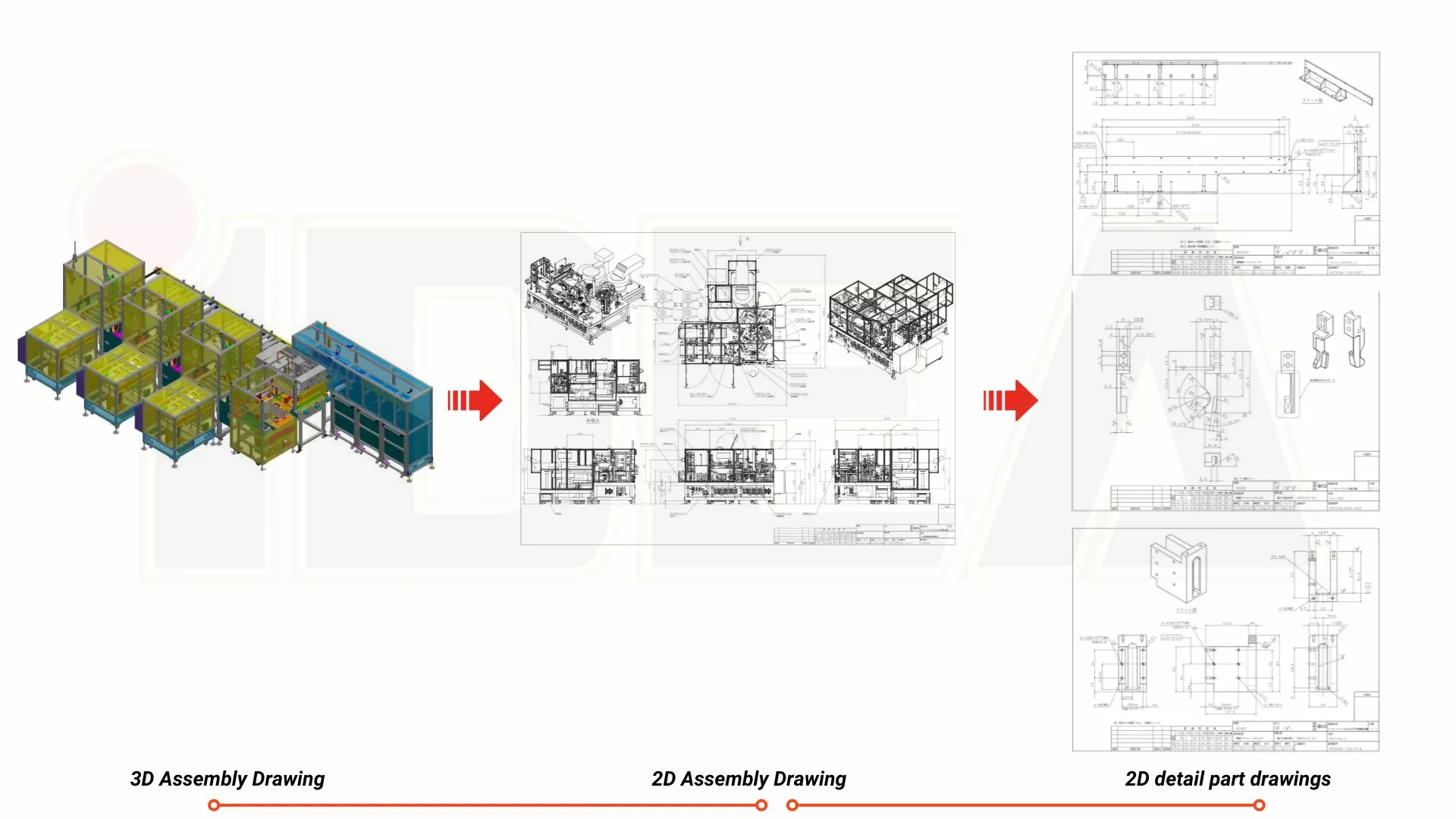
4. 部品図バラシの概要に基づく基本的な標準
-
- ねじ穴、円穴、段付き穴、テーパ穴の標準
図面作成において、「技術標準」の「ねじ標準」に準拠します。
-
- その他の標準部品
部品図バラシの過程では、「技術標準」の「標準部品表」に準拠します。
5. 部品図バラシの手順
5.1 組立図から部品図の分解
-
- 2D組立図からの部品バラシ
AutoCAD、ICAD、CADSUPER などの2D設計ソフトを使用する場合、組立図の投影図から個々の部品を分解します。この方法では、図面の読み取りが難しく、時間がかかる場合があります。しかし、一部の部品が「ブロック(Block)」として保存されている場合、分解作業が容易になります。
また、2Dの組立図から部品バラシを行う際には、寸法の変形や欠落が発生しやすくなります。特に、「標準部品(新販品, 購入品)」が含まれている場合は、必ずその部品の仕様書を確認し、ねじのピッチや取付穴の位置などを正確に把握する必要があります。
-
- 3D組立図からの部品バラシ
SolidWorks、Inventor などの3D設計ソフトを使用する場合、3Dモデルから部品バラシを行います。この方法では、形状の変形が視覚的に確認できるため、2Dよりも精度が向上し、作業時間を短縮できます。
詳しくは、2D・3D バラシサービスについてはこちらをご覧ください。
5.2 図面枠・縮尺の選定
案件によっては、使用する図面枠や縮尺が事前にお客様から指定されている場合があります。その場合は、指示に従い、必要に応じて縮尺のみ調整して作図します。
一方、図面枠や縮尺に関する指定がない場合は、部品のサイズや内容に応じて、作業者が適切な図面枠と縮尺を選定します。最終的に、印刷した際に見やすく、分かりやすい図面になるよう配慮することが重要です。
なお、縮尺はお客様ごとに標準が異なるため、お客様指定の縮尺がある場合は必ずその指定に従う必要があります。特に指定がない場合は、以下の優先縮尺を参考に選定します。
優先縮尺
実寸 | 1:1 |
拡大縮尺 | 10:1 5:1 2:1 |
縮小縮尺 | 1:2 1:3 1:5 1:10 1:20 1:50 1:100 |
非推奨縮尺
拡大縮尺 | 3:1 |
縮小縮尺 | 1:4 1:6 1:8 1:12 1:15 1:30 1:40 1:60 1:1,5 1:2,5 |
5.3 部品の仕様確認
バラシ作業前に、以下の項目を確認する必要があります:
-
- 部品の機能(回転部品、固定部品など)
- 部品の種類(シャフト、ブッシュ、ベースプレート、ブラケット、フレーム、溶接部品 など)
- 組立方法(固定取り付け、他部品への取り付け)
- 材質
- 加工方法、表面粗さ
- 熱処理
- 表面処理
5.4 寸法記入・穴加工指示・その他の注記
部品に寸法を記入する前に、加工基準を明確に設定する必要があります。
この加工基準は、通常、「寸法の基点(原点)」と一致します。この基準設定は非常に重要な作業であり、誤った基準を選択すると、加工精度が確保できず、最悪の場合、組立不良につながる恐れがあります。(基準設定に不明点がある場合は、必ず確認してください。)寸法記入のルールはお客様ごとに異なるため、特別な指示がある場合は必ずその指示に従う必要があります。
一般的には、寸法記入には2つの方法があります:
-
- 段階寸法記入法(ステップ方式)
同じ機能を持つ形状や加工箇所をまとめて連続的に寸法記入する方法です。最もよく使われる方法です。 - 座標寸法記入法
採用するお客様は少数ですが、CNC加工を行うお客様には非常に適した方法です。加工プログラムに直接反映しやすくなります。
- 段階寸法記入法(ステップ方式)
例外ケース
-
- 小物部品や寸法数が少ない部品は、段階寸法記入法が適しています。
- 一方、大型ベースプレートなど、寸法数が非常に多い場合は、座標寸法記入法の方が効率的です。
寸法記入の基本手順
1.外形寸法の記入
2.溶接部品の場合は、溶接前の素材寸法や各プレートの取付位置を記入
3.形状加工寸法の記入(ピン穴やボルト穴を除く)
4.各穴の寸法記入
-
-
- 「穴径、穴種類(ピン穴・ボルト穴)」を明記
- 必要に応じて以下の特記事項も記入(穴深さ、打ち抜き加工指示、ブッシュ圧入指示、裏面加工指示、面取り指示(C面・R面 など)
-
5.フィレット・面取り寸法の記入
寸法記入時の注意事項
-
- ある形状や加工箇所については、必ず一度で全ての必要寸法を記入すること(X方向寸法、Y方向寸法、形状寸法、深さ寸法 など)。
- 同じ寸法を2回記入しないこと(寸法重複禁止)。
- 寸法線の配置は、見やすく、分かりやすいレイアウトを心掛けること。(実際に加工する作業者の立場に立って、見やすい図面作成を意識してください。)
5.5 寸法公差の設定
公差には2種類があります
-
- 寸法公差
- 幾何公差
5.5.1 寸法公差について
図面上に記載されるすべての加工寸法には、実際には必ず公差が存在します。特に、公差の記載がない寸法については、JIS標準公差に基づいて適用されます。一方、標準以外の特別な公差が必要な寸法については、図面上で個別に指示します。
JIS標準公差
公差が記載されていない寸法は、JIS規格の公差表に従って適用します。ただし、寸法が0.5mm以下の場合は、加工内容や部品機能に応じて個別に適切な公差を設定します。
公差の種類
公差の種類は、お客様ごとに異なる基準を設定している場合があります。一般的には、切削加工寸法には「mクラス」の公差、素材切断寸法には「cクラス」の公差を適用するケースが多いです。
特別公差
特別な公差が必要な寸法については、必ず図面上に記載します。具体的な数値は、部品の機能や必要精度によって決定され、お客様仕様として指定される場合もあります。また、以下のように業界標準として定められているものもあります。
代表的な特別公差例
-
- 2つのピン穴の間隔公差(スロット穴を除く):±0.02mm
- ベアリング用ブッシュ穴公差:H7
- ベアリング用シャフト外径公差:h7 または g6
- 軸と穴の嵌合公差:H7/h7
- ピン穴の公差:H7(特別指示がない場合)
5.5.2 幾何公差について
幾何公差に関する具体的な指示は、「技術標準」の「幾何公差基準」を参照してください。
一部の部品や重要寸法については、位置度や平行度など幾何公差の指示が必要です。
例えば、以下のようなケースがあります。
-
- シリンダー、LMガイド、ロボシリンダーなどの取付部には、高精度な平行度公差が求められる。
- シャフト形状部品には、同軸度や真直度が求められる。
- プレート面には、平面度を指示するケースがある。
5.6 表面粗さの指示
表面粗さの指示には2種類があります
-
- 三角記号による指示
- RaまたはRz(単位:µm)による指示
表面粗さの基準
-
-
製品と直接接触する機能面については、非常に高い表面粗さが求められます。この場合、表面粗さは ▽▽▽ (Ra 1.6相当)を基準とします。
-
部品同士が組付けられる接合面については、表面粗さ ▽▽ が基準です。
-
加工面であっても組付けに関与しない面や、重要度が低い面(カバー取付面やセンサーブラケット取付面など)については、表面粗さ ▽(Ra 25〜Ra 12.5相当)が基準です。
-
注意事項
表面粗さをRaで表記する場合、Raの数値は必ず正しく記載し、鏡像反転(mirror)してはいけません。
5.7 溶接部の指示
溶接指示には主に2種類あります:
-
- 溶接位置指示
- 溶接記号指示
場合によっては、上記2種類を併用するケースもあります。
なお、溶接記号の詳細については、「技術標準」の「溶接記号の記載基準」をご参照ください。
注意
溶接記号は鏡像反転(mirror)して表記してはいけません。
5.8 表面処理指示(メッキ・コーティングなど)
部品の材質に応じて、さまざまな表面処理方法が選択されます。表面処理に関する指示は、基本的にお客様からの指定に基づきます。一般的に、鉄やアルミ製の部品は加工後、錆や酸化を防ぐために表面処理が施されます。一方、ステンレス製の部品については、特別な表面処理は不要となるケースがほとんどです。
5.9 熱処理指示
衝撃を受ける部品や、スライド部・製品と頻繁に接触する部品には、耐久性や耐摩耗性を高めるために熱処理が必要となります。熱処理の内容についても、お客様からの指定が基本となります。
5.10 その他の注意事項
上記の指示以外にも、以下のような注意事項が図面上に記載されることがあります。
例:「特に指示のない角部はC0.3~C0.5の面取りを実施」、「曲げ部のRは特に指示がない場合R1とする」など。
これらの指示は、主にお客様の設計基準に基づくものです。
5.11 図面枠情報の入力
図面枠には、以下のような情報を入力します:
機械名、ユニット名、部品番号、部品名、材質、数量、設計者、作図者、承認者、日付、熱処理・表面処理に関する情報など。
なお、一部のお客様からは、これらの情報入力を専用のマクロツールで行うよう指示される場合もあります。
5.12 図面全体の最終チェック
作業完了後、バラシ担当者は図面全体を必ずチェックします。すべての情報に漏れがないかを確認する必要があります。お客様指定のチェック項目に加え、基本的には以下のような社内チェックリストに基づいて確認を行います。
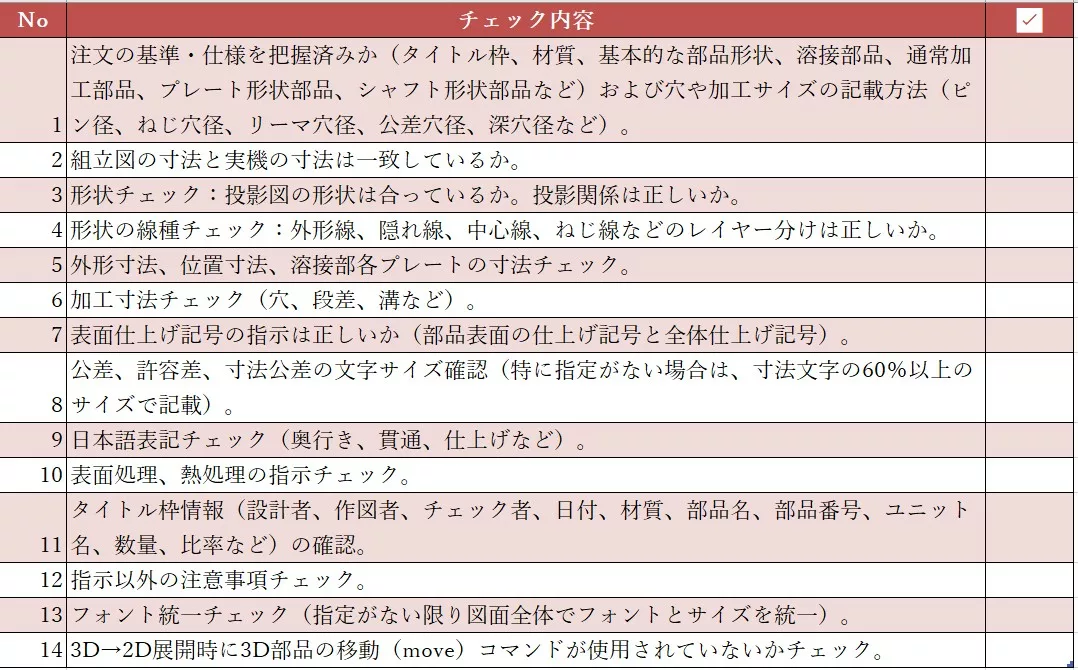
5.13 部品図バラシのプロセスを確立する
上記では、部品図バラシを行う際に必要な作業内容を説明しました。しかし、最も効率的かつ正確に図面を作成する方法も重要なポイントです。
部品バラシをスムーズに進めるためには、明確なプロセスを確立することが不可欠です。バラシ作業のプロセスとは、各工程を体系的にまとめた手順書であり、作業を順番に進めることで、抜け漏れやミスを防ぐことができます。
部品の詳細情報を確認し、変形を理解し、分解作業を終えた後にバラシの手順を決定します。この手順は、頭の中で整理することもできますが、可能な限り紙に書き出すことを推奨します。最初は少し時間がかかりますが、慣れてくるとスピードが向上し、作業の正確性も向上します。
基本的なバラシの手順
1.図面枠の選定と部品の配置
2.部品の変形処理と線種の整理
3.断面図・投影図の追加(必要に応じて)
4.外形寸法の記入、表面粗さ記号の追加(必要に応じて)
5.加工形状の寸法記入、公差・表面粗さの追加(必要に応じて)
6.穴の寸法記入、公差、注記、表面処理指示の追加(必要に応じて)
7.図面枠の情報入力
8.図面枠外の注記追加(必要に応じて)
9.最終チェック(チェックリストに基づいて確認)
部品の種類や複雑さによって、上記の手順を柔軟に調整することが重要です。また、作業の流れを標準化することで、一貫性のある作業が可能となり、効率的かつ正確なバラシを実現できます。
バラシプロセスを確立する重要性
明確なバラシ手順がない場合、作業中に迷いや判断ミスが発生しやすくなります。「この部分はどうするべきか?」と都度考えていると、作業が遅くなり、ミスが増え、生産性が低下する可能性があります。そのため、最適なバラシ手順を確立し、効率的な作業フローを確保することが重要です。
「部品図バラシの概要(パート1)」もぜひご参照ください。