はじめに
現代の製造業では、製品の耐久性を向上させ、適切なメンテナンス計画を策定することが求められています。そのために活用されているのが「動作シミュレーション」です。本記事では、動作シミュレーションを活用した製品寿命予測とメンテナンス計画の最適化について詳しく解説します。
動作シミュレーションとは?
動作シミュレーションとは、製品が実際に使用される環境下での動作をコンピュータ上で再現し、その性能や耐久性を評価する技術です。
シミュレーションを用いることで、以下のような利点があります。
- 試作コストの削減:物理的な試作を減らし、コストを抑える。
- 耐久性評価:負荷や摩耗の影響を事前に分析できる。
- メンテナンス計画の最適化:最適な点検時期や交換部品の推奨が可能になる。
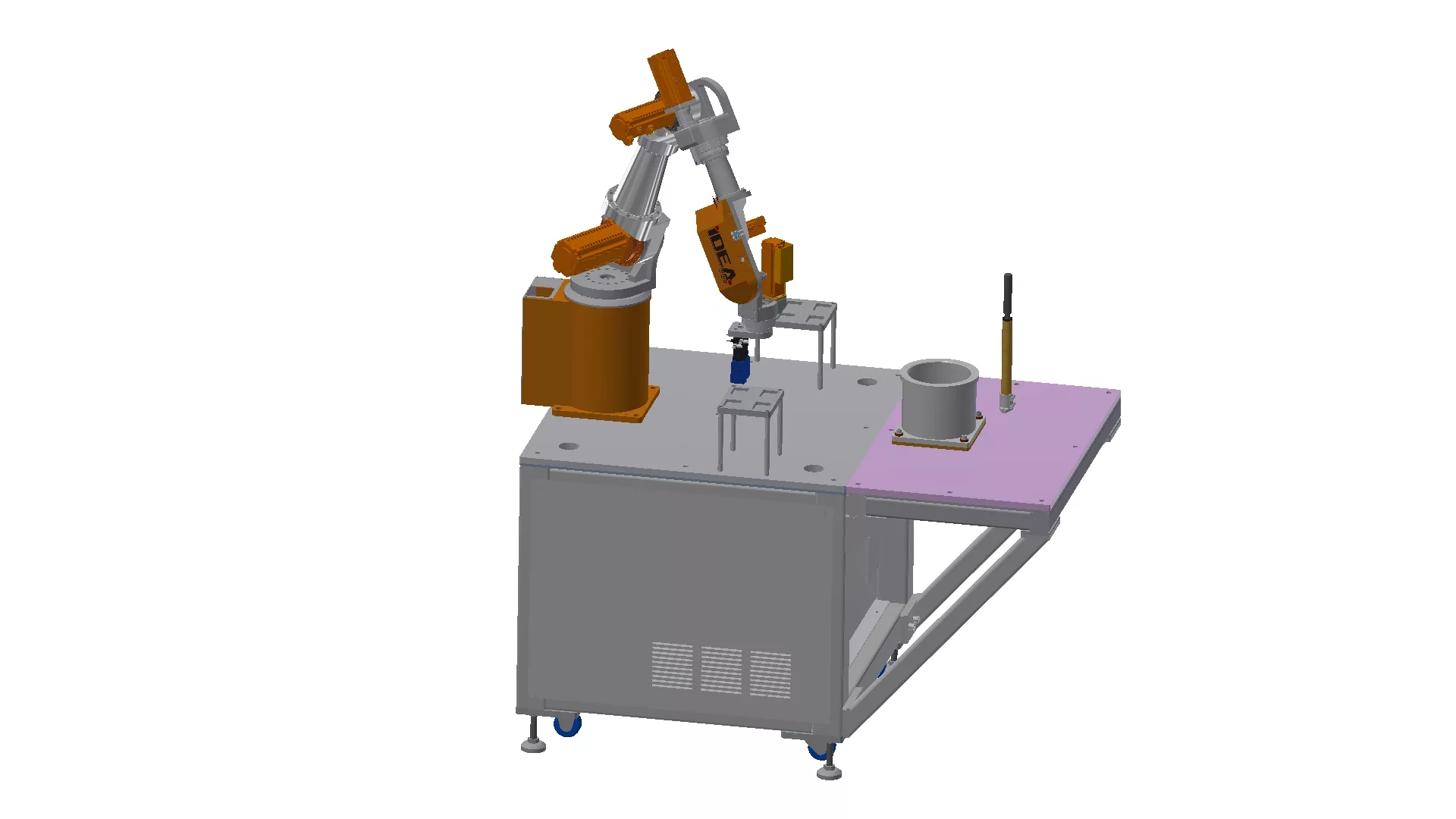
動作シミュレーションを活用した製品寿命予測
1.製品寿命予測の重要性
製品の寿命を正確に予測することで、企業は保証期間を適切に設定し、製品の信頼性を向上させることができます。また、ユーザーにとっても、適切なメンテナンススケジュールを確立する手助けになります。
2.製品寿命を左右する要因
- 環境要因:温度、湿度、振動など。
- 使用条件:負荷の大きさ、動作頻度。
- 材料の劣化:摩耗、腐食、疲労破壊。
3.動作シミュレーションによる寿命予測プロセス
- CADモデルの作成:3D設計データを用意。
- 物理的条件の設定:負荷、摩擦、温度などを考慮。
- シミュレーション実行:有限要素解析(FEA)やマルチボディダイナミクス(MBD)を用いる。
- データ解析:摩耗や応力集中の発生箇所を特定。
- 寿命評価:期待寿命を算出し、メンテナンス時期を決定。
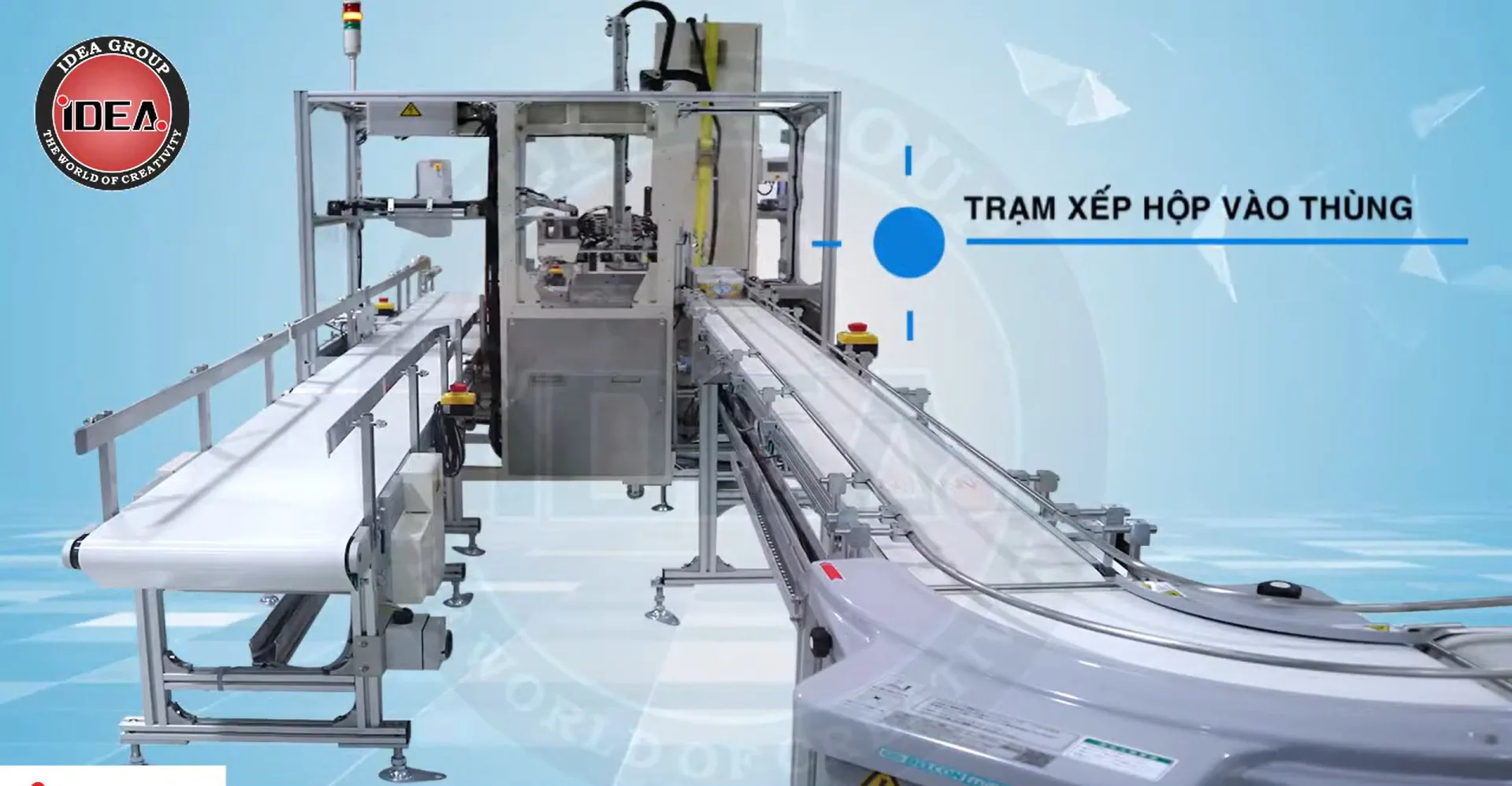
メンテナンス計画の最適化
a.予防保全 vs 事後保全
従来の事後保全(故障後の修理)では、突発的なダウンタイムが発生し、コストが高くなります。一方、動作シミュレーションを活用すれば、予防保全(故障する前にメンテナンスを実施)が可能になります。
b.動作シミュレーションによるメンテナンス最適化手法
- 異常検知:シミュレーションデータを基に、異常発生の兆候を検出。
- 最適な交換時期の算出:寿命予測に基づいて、部品交換の最適タイミングを特定。
- コスト削減:不要なメンテナンスを削減し、必要な保守作業のみを実施。
c.事例紹介:自動車産業における適用
近年、自動車メーカーではエンジンやトランスミッションの寿命を動作シミュレーションで予測し、適切なオイル交換時期や部品交換計画を立案しています。これにより、メンテナンスコストを削減し、車両の信頼性を向上させています。
動作シミュレーションの未来と展望
今後、AIや機械学習と連携することで、動作シミュレーションはより精度が向上すると考えられます。また、IoTと組み合わせることで、リアルタイムでの寿命予測や自動メンテナンス計画の策定も可能になるでしょう。
まとめ
動作シミュレーションを活用することで、製品の寿命予測が精度高く行え、メンテナンス計画の最適化が実現できます。企業にとってはコスト削減と品質向上の両方を実現できるため、今後ますます重要性が増す技術となるでしょう。
今後の技術進化に期待しつつ、貴社の設計・保守プロセスに動作シミュレーションを導入してみてはいかがでしょうか?
IDEAテクノロジーは、製品設計から動作シミュレーション、メンテナンス計画の最適化まで幅広いサービスを提供し、最適なシミュレーションソリューションをご提案いたします。